Johannes Dirnberger-Wild is a university lecturer at the Institute of Industrial Management and has been working at FH JOANNEUM since 2016 with a focus on business process management, supply chain management and logistics. Dirnberger-Wild completed his Master’s degree in Industrial Management at FH JOANNEUM and as part of a double degree at the University of Udine, where he is currently also working on his doctorate on the digitalization of procurement processes. In this Science Story, he looks at the optimization of workflows.
I recently came across an online posting by the German satirist El Hotzo and I was particularly amused by the statement "the workflows were not optimized".
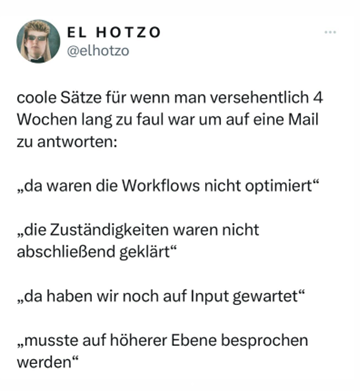
On the one hand, because El Hotzo cites it as an example of a standard excuse - and as such it may well be convincing. On the other hand, it's true and often "the workflows" really are to blame if you wait a long time for something at work.
Let's take the processing of a business trip request as an example. If it takes four weeks to know whether the planned trip abroad to the supplier is approved or has to take place online, it is simply a "non-optimized" workflow. Therefore, even if satire is characterized by exaggeration and irony, the truth of the quoted statement is greater from a process management perspective than one might initially assume.
From internship to specialization in business process management
I discovered my passion for business process management during my studies at FH JOANNEUM. It's not about accepting poorly designed and/or faulty processes or workflows, but about improving them (explanation in the notebox at the end). During my practical semester, I worked for an international company in Munich. From there, I traveled to London, Düsseldorf, and Naples to first collect information on the processes of the service providers and suppliers through interviews and present them in the form of graphical process models. I then analyzed these models for weaknesses and developed improvement measures together with the people involved.
Between productivity and daydreaming
It was then that I began to realize what research also frequently points out: poorly coordinated, long processes are not only expensive and make customers dissatisfied, but also employees. When studies show that full-time employees are only really focused and "productive" part of the time because they spend up to two hours a day searching for work-related information, the cause is less to be found in their work attitude and more in the organizational and technical framework conditions. And if over 90 % of us daydream during meetings, this is hardly surprising: who has never spent time in an unnecessary meeting while an important task had to be left undone?
From improved framework conditions to higher satisfaction and productivity
So today, more than ten years later, when I deal with process management in teaching, projects and research at FH JOANNEUM, my main motivation is still to make a contribution to improving the framework conditions. I am convinced that it makes us happier and more productive overall if we invest our precious time wisely. This requires both organizational measures, such as only scheduling necessary meetings and making them efficient (good preparation, moderation, and time discipline), as well as technical solutions, such as automating a tedious task in which data is manually transferred from one system to the next. Suddenly, employees could spend most of their time at work on activities that have a customer benefit. For example, having to do less administrative work and being able to advise customers more intensively on site or having more time available for creative tasks such as developing new products or business models. As someone who also plays music in a band and is familiar with creative processes in which you spend hours working on a song without even looking at your watch, I can't overestimate the opportunities and qualities that "optimized workflows" can offer us on the job from this perspective. And productivity increases can also make a significant contribution to solving the worsening shortage of skilled workers, one of the greatest economic challenges of our time, as economist Marcel Fratzscher explains in the current edition of "Das Politikteil" podcast from February 2.
4 weeks? Then it probably wasn't that important...
Therefore, my conclusion is that the four-week-long unanswered email to which El Hotzo alludes at the beginning was obviously unimportant, because otherwise someone would have asked. And from this point of view, I don't see this example as a "lame excuse", but as a wake-up call to devote precious personal time to more meaningful things than an unnecessary email.
Sources: Productivity Statistics: Key Elements in 2023 | TeamStage
Processes
are based on recurring procedures with which companies achieve desired results. For example, producing a smartphone that always has the same properties.
Workflows
are more detailed processes that are often IT-based. For example, a business trip request that is submitted in a system and then automatically forwarded for processing, without any additional emails or phone calls.
Business process management
comprises the systematic and continuous design, monitoring, control, and further development of all business processes.