Das Josef Ressel Zentrum für Zeitreihenbasierte Fehlervorhersage und -vermeidung wird von der Christian Doppler Forschungsgesellschaft und dem Bundesministerium für Arbeit und Wirtschaft unterstützt. Unternehmenspartner sind AVL DiTEST und voestalpine Tubulars.
Josef Ressel Zentrum für Zeitreihenbasierte Fehlervorhersage und -vermeidung
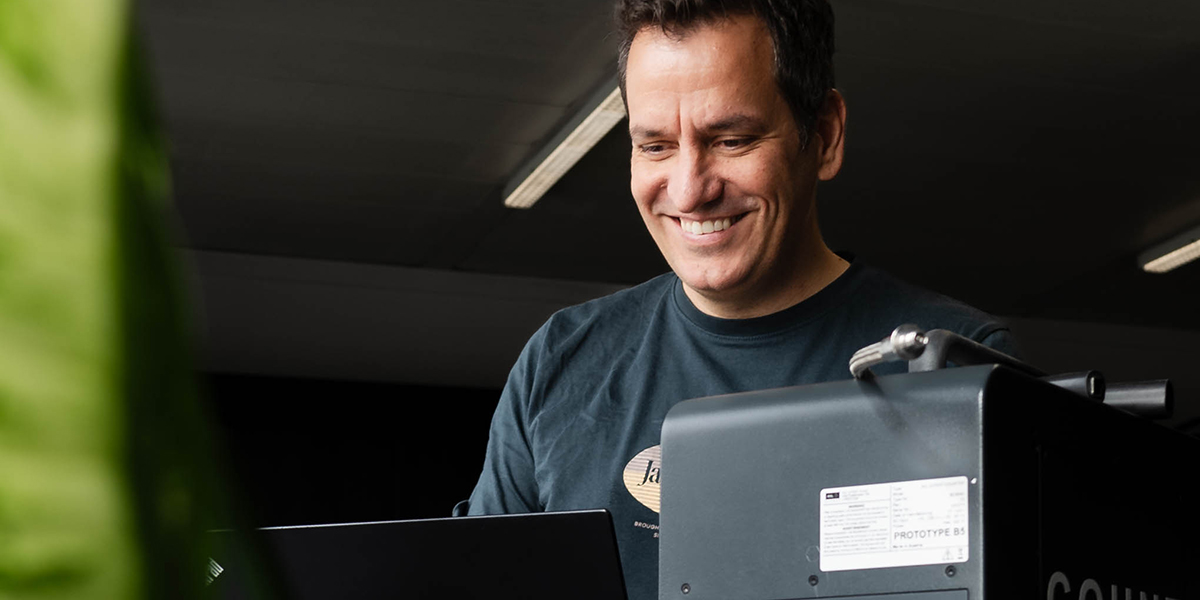